弱点と課題を克服、実用化へ大きな一歩。
世界最高レベルの磁気特性を実現。
磁性粉末をプラスチック、樹脂、ゴムなどに練り込んで成型した磁石を「ボンド磁石」といいます。たとえば自動車の初心者/高齢者マークや冷蔵庫に貼れるステッカーなどもその一種(ラバーマグネット)。ボンド磁石は、高い形状自由度が特長です。
サマリウム-鉄-窒素系磁石は、600℃ほどの温度で分解してしまうため焼き固めること(液相焼結)ができず、その微粉末を樹脂と混ぜ合わせたボンド磁石として用いられています。しかし、150℃以上で保磁力が低下してしまい、期待する性質が得られないという欠点があります。私は(1)原料としてのサマリウム-鉄-窒素系微粉末の特性向上、(2)新規製造プロセスによるサマリウム-鉄-窒素系バルク磁石の開発、という2つのアプローチによりこの課題多き磁性材料に挑んできました。
サマリウム-鉄-窒素系磁石の耐熱性を向上させる方法の一つにマンガン(Mn)添加があります。実際に大きく改善されるのですが、他方では磁石性能(最大エネルギー積(BH)max)の低下を招いてしまうのです。まさに一得一失ですね。そこで私は、サマリウム-鉄-窒素系微粉末にマンガンを混ぜ合わせるのではなく、母合金粉末の表面にのみ濃く行き渡らせることで、磁化の低下を抑制しつつ、高耐熱性も得られるのではないかと考察しました。2ステップ還元拡散法という新しい粉末作製プロセスの開発により、マンガンの表面濃化に成功し(コアシェル構造の形成)、優れた磁気特性を発現させることに成功しました。このプロセスは世界初です。
一方、サマリウム-鉄-窒素系磁石の保磁力が低下する主要因は酸化とみられてきましたが、その詳細は未解明でした。私たちの研究室では微細組織の観察により、焼結の熱処理中に磁粉表面の酸素が拡散分解することでアルファ鉄(α-Fe)相が生成される界面反応メカニズムを明らかにしました。サマリウム-鉄-窒素系磁石の性能・特性向上の鍵の一つが作製プロセスの「低酸素化」です。私たちは磁石粉末の作製から磁石化、低温焼結まで、すべての作製工程を完全大気非暴露環境で行うプロセスを構築し、世界最高レベルの高磁気特性を持つサマリウム-鉄-窒素/亜鉛系のバルク磁石を実現させました(図/写真2)。サマリウム-鉄-窒素系磁石はバルク化が困難であることは先に述べましたが、本研究・開発は工業的な作製プロセスを視野においたものであり、実用化へ大きく前進したといえます。
このサマリウム-鉄-窒素系磁石以外にも、薄膜や複合ナノ粉末など様々な技術を駆使して、未だ世の中にない新規磁石の探索にも取り組んでいます。
…と、駆け足で取り組みとその成果を紹介してきましたが、もちん一朝一夕に成せるものではなく、ありとあらゆるアイデアを試しては空振りに終わり、失敗を踏み台にしてまた新たな方法を模索するという繰り返しでした。しかし、わからなかったことが少しずつ明らかになっていく、不可能と思えたことに手ごたえを感じるという小さな実りの積み重ねが、研究・開発の歩みを前に進める原動力になっています。さらには論文を発表することによって、世界の研究者コミュニティから健全に評価され、フィードバックをいただくことも士気や意欲につながっています。
幸いにも日本は先達の功績と伝統により、永久磁石の分野では世界で先導的な役割を果たしています。しかし、近年では研究・開発の国際競争も激しくなっています。新規性や独創性あふれるアイデアで、磁性材料の新しい地平を切り拓くとともに、これからの低炭素社会に資する新しい材料探索/創成に挑戦していきます。
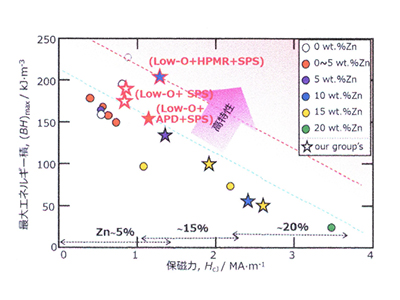
(図/写真2)低酸素なSm-Fe-N系粉末に、水素プラズマ-金属反応法(HPMR)等により作製した低酸素・微細Zn粉末を混合することで、低酸素Sm-Fe-N/Zn混合粉末を作製。その混合粉末を放電プラズマ焼結法(SPS)で焼結することで、世界最高レベルの高磁気特性を持つSm-Fe-N系バルクマグネットを実現した。上記、〇で示されているのは既報値、☆は松浦先生らの報告値。
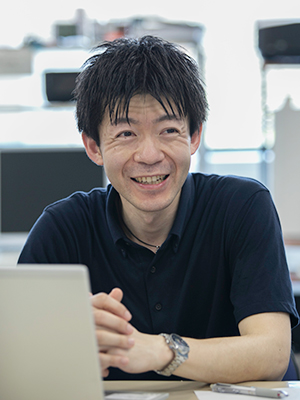
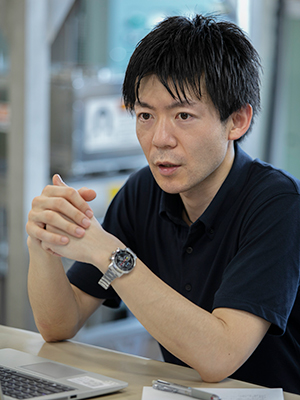
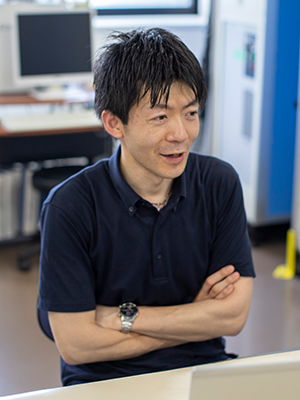
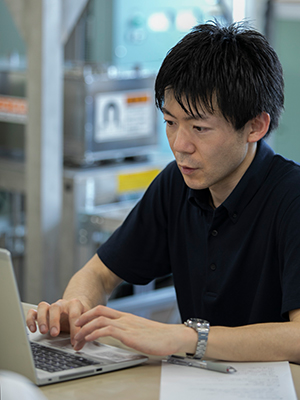
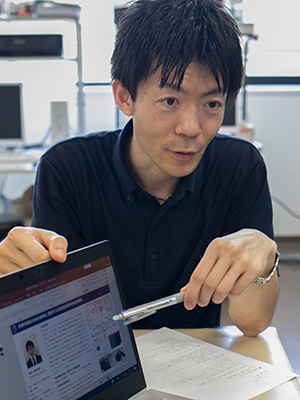
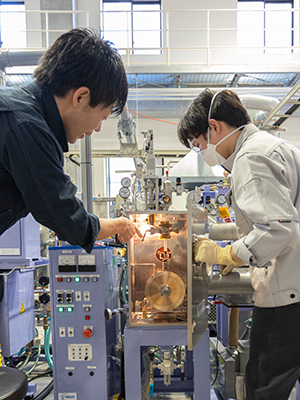